Training for Manufacturers in Kent & throughout the UK.
Simply click on the tabs to see more detail on the courses you are interested in. If you have any questiuons or queries we'd be happy to help, so please use the contact button at the bottom of each course description or call us on 01843 621138
Lean
Lean Awareness - 1 day
Participant
All Employees
Overview
This one-day training workshop introduces the main principles and techniques of Lean Thinking. It is a very interactive workshop relevant to all employees and incudes a number of practical activities designed to engage, motivate and inspire.
Topics Covered
Lean Principles, Value and waste, 8 Wastes, 5S Workplace organisation and visual management, Lean simulation exercise, Line balancing, SQCD KPI's.
Learning Objective
1. To appreciate the difference between value added and non value added activity or Waste. 2. To understand how Lean thinking, 5S and visual management techniques can help the organisation meet Safety, Quality, Cost and OTIF objectives. 3. To understand both individual and team responsibilities relating to 5S workplace organisation and good housekeeping.
Learning Outcomes
All participants will understand the fundamentals of lean thinking and how the application of lean principles can drive performance. They will also be able to identify both value added steps and waste within a given process. They will be able to introduce and / or maintain effective 5S and Visual Management within their own work areas and fully appreciate their own role in delivering expected SQCD outcomes.
Duration
1 day
Lean Facilitator Programme - 5 days
Participant
Lean Champions, Team Leaders and Engineers.
Overview
The programme participants will explore the proven tools, techniques and skills used in ‘Lean’ in an interactive setting supported by exercises, case studies and discussion to develop ‘Facilitation’ skills. Each topic is related to real world business scenarios and participants are encouraged to raise their own specific issues & opportunities for discussion. During the five day programme participants will learn about the full range of Lean tools as well as the soft skills required to engage others in continuous improvements.
Topics Covered
Change / Why Change, PDCA Deming cycle, Lean Principles, Value and Waste, Lean Simulation Chaos to flow plug factory, Kanban, Line Balancing, Takt time,5S Workplace organisation and visual Management, Value Stream Mapping, OEE, SMED,TPM,Mapping and data capture, FMEA, Team problem solving, Team Roles, Problem solving techniques, SPC,Learning Styles, Designing training materials, Objective setting, Presenting and facilitation, running exercises, encouraging discussion, developing action plans, types of training evaluation.
Learning Objective
"1. To gain a clear understanding of Lean principles and learn how to select and apply the relevant tools and techniques.
2. To appreciated how best to drive change and lead Lean and continuous improvement projects, to bring measurable benefit to your organisation.
3. Understand how to present your ideas, motivate and train other team members and engage them in improvement activity. "
Learning Outcomes
At the end of the programme participants will have the confidence to lead a CI project, select appropriate lean tools and engage and lead others to deliver successful CI Projects. Participants will put learning into practice by scoping, implementing and delivering an improvement project (of the business’s choice) back in the workplace – a real project delivering real results.
Duration
5 days
Lean Six Sigma
Lean Six Sigma Green Belt - 9 days
Participant
Mangers, Team Leaders and Engineers
Overview
"The practical application of Six Sigma will remove variation and waste
from a wide variety of complex business processes. The methodology is project focused and delivers bottom line results fast. It is specifically designed to dovetail with any Lean approaches that are already being used to enhance and multiply the results. Typical benefits include - Improving reliability, Reducing reject rates, Improving consistency, Simplifying technical and ‘complex’ processes.
"
Topics Covered
"Process improvement – using a structured approach to analyse processes to sustain quality and control new processes.
Statistical Process Control (SPC). DMAIC (define, measure, analyse, improve and control ) – with a strong focus on analyse and Improve. Variation – explore how variations can effect quality and learn how to reduce this and achieve predictable outcomes. Defects – preventing, identifying and controlling.
"
Learning Objective
1. To establish a clear understanding of all the components of Six Sigma. 2. To appreciate how to select and apply each element of the Six Sigma methodology. 3. To be able to lead a Six Sigma project from start to end
Learning Outcomes
The participants will apply what they have learned to a chosen area within their organisation. They will present their project to an external panel which includes a very experienced Master Black Belt who will validate their competence level before they become formally Six Sigma Green Belt certified.
Duration
9 days
Lean Six Sigma Black Belt - 3 days
Participant
Mangers, Team Leaders and Engineers
Overview
"The practical application of Six Sigma will remove variation and waste
from a wide variety of complex business processes. The methodology is project focused and delivers bottom line results fast. It is specifically designed to dovetail with any Lean approaches that are already being used to enhance and multiply the results. Typical benefits include - Improving reliability, Reducing reject rates, Improving consistency, Simplifying technical and ‘complex’ processes.
"
Topics Covered
Design of Experiments (DOE). Hypothesis testing – use statistical analysis to ascertain whether differences between two samples are random chance or true differences. Strategic planning and CI leadership.
Learning Objective
1. To master the application of DOE (Design of Experiments) 2. To gain an advanced knowledge and understanding of statistical analyses and Hypothesis testing. 3. Have the capability to develop, lead and deliveer a Six Sigma strategy for the business and lead a company wide programme to reduce variability
Learning Outcomes
Participants will be able to apply what they have learned to highly complex quality and/or variability issues within their organisation. They have the ability to develop a clear strategy and tactical plan to apply Six Sigma to drive significant measurable improvement and bottom line benefits. They will present their project to an external panel which includes a very experienced Master Black Belt who will validate their competence level before they become formally Six Sigma certified.
Duration
3 days
Leadership and Management
Leadership and Management Programme - 5 days
Participant
Managers and Team Leaders
Overview
This programme will allow participants to underpin practice with management and leadership theory/current research. This will encourage reflection on knowledge acquired, and how to apply and implement within real world business situations. The 5 day programme builds skills and confidence by layering management foundation and skills. The topics covered provide a wide range of practical tools to enable confident management and leadership of people and teams.
Topics Covered
Managing change, Giving & receiving feedback, Building a team, Motivating & Developing Others, Being a Good Coach, Time Management, Setting Objectives & Delegating Effectively, Managing Performance, Managing Conflict
Learning Objective
"1. Understand what is meant by management and managerial effectiveness
2. Identify the roles which are fulfilled while working as a manager or team leader.
3. Identify methods to develop and enhance individual and team performance
4. Identify leadership and managerial activities that contribute to being an effective team leader or manager
5. Understand time pressures and the need for time management"
Learning Outcomes
"After completing the modules participants should be able to:
1. Reflect critically on their own practice as a manager or team leader, evaluating strengths and weaknesses and identifying strategies for developing themselves and their teams to increase personal and organisational effectiveness.
2. Demonstrate the practical ability to analyse complex managerial/leadership situations taking into account multiple interests and potential barriers.
3. Demonstrate increased professional effectiveness to confidently achieve organisational objectives and successfully engage and lead individuals and teams. "
Duration
5 days
Building a High Performance Team - 1 day
Participant
Managers and Team Leaders
Overview
"The high performance teams course is designed to help managers and team leaders develop the knowledge and skills to create and maintain a high performance team.
We will utilise the Belbin Team Roles model and self perception inventory to raise self awareness of participant’s preferred team role within a team, as well as the other behavioural characteristics that need to be present to achieve a high performing team.
Participants will also learn techniques that will engage and inspire their teams to achieve a higher level of team performance and synergy."
Topics Covered
Team Role Theory, Belbin's team roles, Team engagement in problem solving. High Performance team Characteristics.
Learning Objective
"1. Identified strategies to manage the different behavioural roles people take within a team and ways to improve team dynamics
2. Established personal strategies and actions that will build and maintain a high performing team
3. Communicated their own team vision in an engaging way to encourage team member “buy in"
Learning Outcomes
Participants will be able to identify their own team role behavioural preferences and also that of their team members. They will be able to inspire, motivate and engage their team to work together as an effective unit.
Duration
1 day
Quality
Quality Fundamentals, SPC and FMEA - 1 day
Participant
Operatives / Engineers
Overview
This introduction to quality, SPC and FMEA provides a solid foundation covering key quality principles and concepts. In addition delegates will have the opportunity to apply quality tools and techniques to processes and quality issues relative to their own work environment. The course can cover both Process and Design FMEA and the content is weighted according to the audience.
Topics Covered
The eight dimensions of quality, The 7 Quality Tools, Critical to Quality tree, SPC, Controlling variability, Basic problem solving techniques, Preventing cost of poor quality. Process FMEA, Design FMEA
Learning Objective
1. To gain a broad understanding of Quality fundamentals and how they apply to their working environment. 2.Learn how SPC and other Quality tools can be applied to improve quality by reducing variability. 3. Understand how FMEA can be applied to establish potential process failures and apply relevant control measures.
Learning Outcomes
Participants will be able to use a broad range of tools to effectively analyses quality problems. Gather data and establish relevant corrective action and process control measures. They will also be able to analyse any process or design using FMEA, establish quality improvement priorities to reduce the risk of failure and establish relevant control measures within a given process or product design.
Duration
1 day
Practical Problems Solving
- 1 day
Participant
Operatives / Engineers
Overview
The course applies the 8D process in a very practical way. With over 200 learners trained using this method. Our unique and very hands on problem solving exercise is a fun way of learning and has proven to be a very effective learning process. This one-day course provides a detailed understanding of a rapid, structured problem- solving process, which delivers long term solutions. Delegates will use linked tools and practical examples to become more familiar with the key stages of problem definition and solution.
Topics Covered
8D problem solving process, Problem definition, Data gathering and analysis techniques, Containment actions, 5 Whys, Fishbone / Cause and effect root cause analysis, Run Charts, Permanent corrective action.
Learning Objective
"1. Understand 8D problem solving methodology.
2. Learn how to apply 8D to a practical problem using the 8D process correctly, applying relevant quality tools.
3. Recognise the importance of gathering and analysing data. "
Learning Outcomes
On completion of the course, participants will be able to apply the 8D process in a practical way, gathering and analysing data and apply alternative techniques to establish the root causes and implement solutions to problems that will prevent reoccurrence.
Duration
1 day
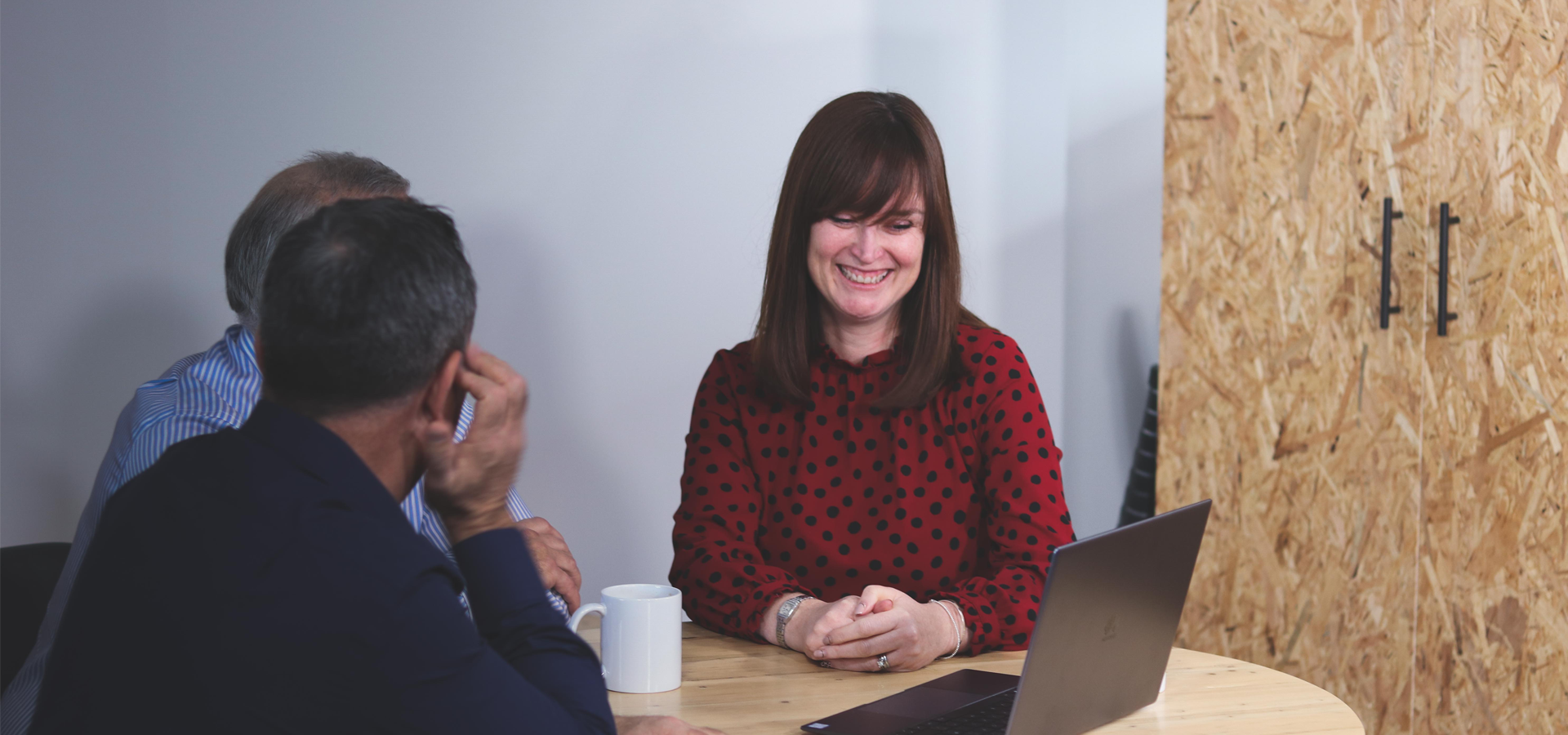